
Alloy jaws are essential tools in various industries due to their durability and precision. From jewelry making to mechanical applications, alloy jaws offer a versatile solution for securing materials firmly during processing. However, the importance of safety when using these potent tools cannot be overstated. Understanding potential hazards, adhering to industry standards, and following best practices can significantly mitigate risks associated with improper use.
Personal Protective Equipment (PPE)
When working with alloy jaws, personal protective equipment (PPE) is your first line of defense against injury. Essential PPE includes gloves, goggles, and protective clothing. Gloves protect hands from sharp edges and hot surfaces, while goggles shield eyes from debris and splinters. Wearing the appropriate PPE not only safeguards you from immediate harm but also prevents common injuries such as cuts, abrasions, and eye damage.
The significance of wearing proper PPE cannot be overemphasized. Many workplace injuries occur due to negligence in this area, underscoring the need for consistent and correct usage of all recommended gear. Make sure to check the condition of your PPE regularly and replace any worn-out items promptly.
Workspace Preparation
A well-prepared workspace significantly reduces the risk of accidents. Ensure that your work area is clean and organized, minimizing clutter that could lead to trips or falls. Adequate lighting is crucial for visibility; poor lighting increases the likelihood of mistakes. Good ventilation is equally important, particularly if you're working in an enclosed space where fumes or dust might accumulate.
Proper storage of alloy jaws and related tools is another critical aspect of workspace preparation. Store them in designated areas that are easily accessible yet secure, preventing accidental displacement or damage.
Inspection of Alloy Jaws
Before utilizing alloy jaws, conducting a thorough inspection is paramount. Check for any signs of wear and tear, such as cracks, chips, or deformities, which could compromise their functionality. Identifying defects before they become hazardous helps avoid unexpected failures during use.
Regular maintenance and adherence to inspection schedules ensure longevity and reliable performance of your alloy jaws. Keeping detailed records of inspections can help track the lifespan and highlight recurring issues that may need addressing.
Proper Handling Techniques
Safe handling starts with understanding the correct methods for lifting and transporting alloy jaws. Use both hands for larger or heavier pieces, and maintain a firm grip to prevent slipping. Employ ergonomic techniques to minimize strain on your back and muscles. Secure grips are vital; dropping alloy jaws can cause significant injury or damage to other components.
Techniques like maintaining a straight posture when lifting and avoiding sudden movements contribute to safer handling. These precautions help reduce the risk of musculoskeletal injuries commonly associated with manual handling tasks.
Usage Best Practices
Using alloy jaws safely requires paying attention to several key steps. Always follow the manufacturer’s instructions specific to your tool model. Align materials correctly within the jaws to ensure uniform gripping pressure. Avoid applying excessive force beyond what the alloy jaws are rated for, as this can lead to breakage.
Common mistakes include using damaged jaws, neglecting regular cleaning, and ignoring minor damages that can escalate into larger problems. Dedicating time to learn and practice these best practices fosters a safer working environment.
Emergency Procedures
Accidents can still happen despite best efforts, so it's crucial to have emergency procedures in place. Familiarize yourself with the steps to take in case of an accident, including shutting down machinery if necessary and contacting emergency services. Immediate first aid measures, such as rinsing out an eye or dressing wounds, can prevent complications.
An established emergency plan should be known to everyone in the workspace, ensuring quick and efficient responses when needed. Regular drills and training sessions help keep everyone prepared and aware of their roles during emergencies.
Training and Continuous Learning
Proper training and certification for using alloy jaws are integral to workplace safety. Investing time in learning how to handle these tools properly pays dividends in the long run by reducing incident rates. Various resources, such as online courses, workshops, and manuals, provide valuable information for skill enhancement.
Encouraging a culture of continuous learning promotes ongoing safety improvements. Share knowledge and experiences with colleagues to collectively elevate the standard of safety in your workplace.
Conclusion
Prioritizing safety when using alloy jaws translates to healthier and more productive work environments. By consistently employing PPE, preparing your workspace, inspecting tools, utilizing proper handling techniques, and following best usage practices, you can significantly reduce risks. Always be ready for emergencies and commit to continuous learning to stay updated on safety protocols. Remember, safeguarding oneself through diligent application of safety measures benefits both individuals and organizations alike.
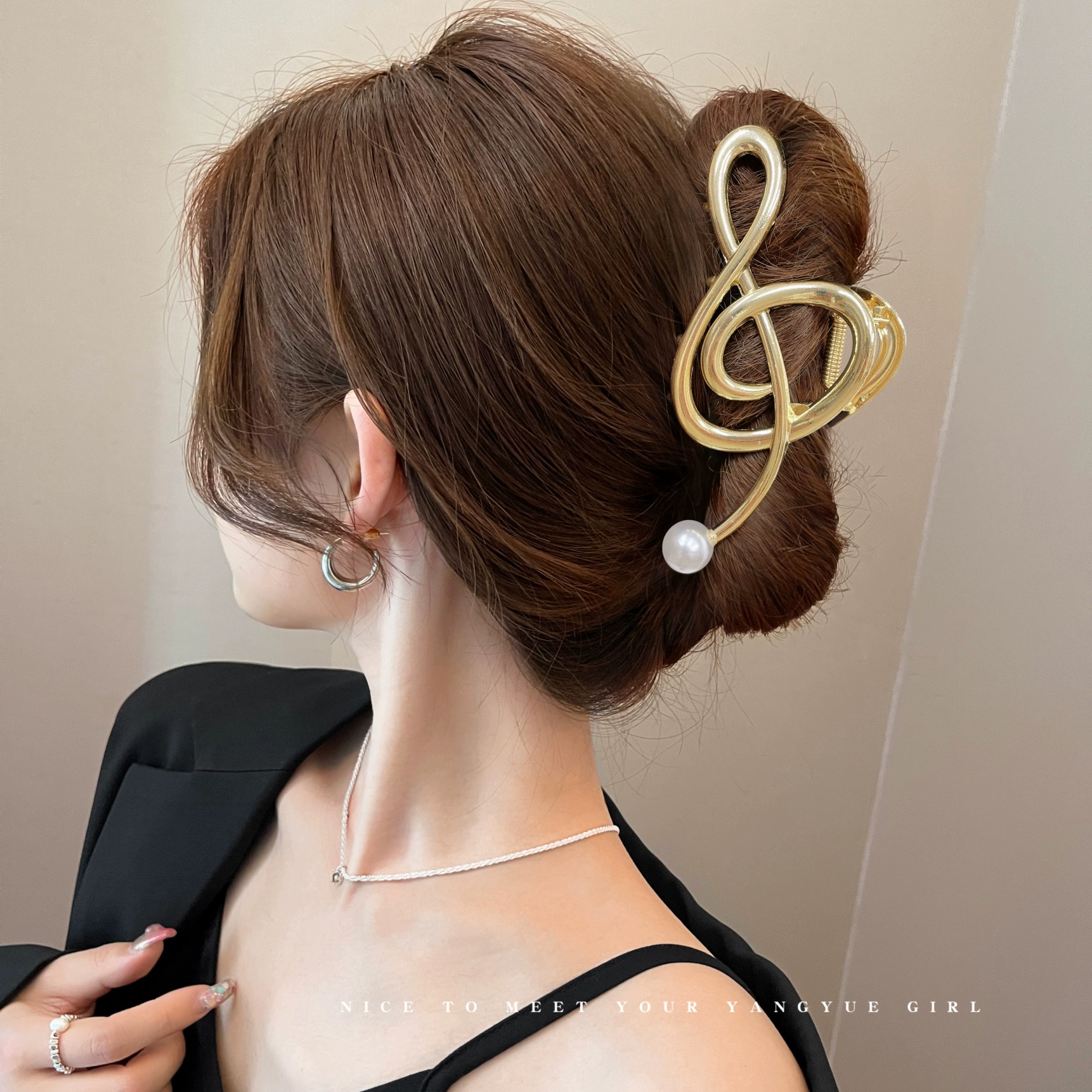