
Understanding Alloy Jaws
Alloy jaws are essential components used across various industries, particularly where precise mechanical grip and functionality are required. These specialized tools are crafted from blended metals to provide greater strength, durability, and resistance to wear compared to traditional materials. Common applications include machinery, automotive parts, and even high-stress environments like manufacturing plants and construction sites.
Identifying Common Problems
The longevity and performance of alloy jaws can be compromised by several issues. Recognizing the signs early on helps mitigate more substantial damages and prolongs the life of the equipment.
Signs of Wear and Tear
Visual indicators: Discoloration, cracking, or obvious deformations are immediate red flags that suggest significant wear. Surface scratches and abrasions might also indicate that the material is beginning to degrade.
Performance-related symptoms: Decreased efficiency, irregular movements, or unexpected noises during operation often signal underlying problems with the jaws' condition.
Misalignment Issues
Misalignment occurs when the alloy jaws deviate from their intended position, leading to inefficient operation and potential damage.
Causes of misalignment: Repeated heavy use, poor installation, or inadequate maintenance practices can lead to this issue.
Diagnostic methods: Regularly checking alignment using precision instruments or comparing the functional benchmarks against manufacturer specifications can help detect misalignments early.
Material Fatigue
Over time, repeated loading cycles cause microscopic cracks within the alloy, which gradually grow and exacerbate wear.
Early warning signs: Minor fractures, subtle distortions, and slight decreases in performance may hint at imminent material fatigue.
Long-term effects on performance: Ignoring initial signs can lead to catastrophic failure, resulting in costly downtime and repairs.
Frequent Causes of Issues
Several factors contribute to the degradation of alloy jaws, understanding these can aid in preventive measures.
Improper Maintenance Practices
Poor maintenance routines significantly impact the lifespan and efficacy of alloy jaws.
Neglect vs. over-maintenance: Both neglecting regular upkeep and excessively servicing the equipment can be detrimental. While the former allows for unaddressed wear, the latter could lead to premature material stress.
Best practices for regular upkeep: Follow manufacturer's guidelines for lubrication, cleaning schedules, and periodic inspections.
Environmental Factors
The surrounding environment affects how well alloy jaws perform under certain conditions.
Influence of temperature and humidity: High temperatures may accelerate wear, while moisture can lead to corrosion if not adequately protected.
Protective measures: Utilizing environmental controls such as protective coatings and maintaining optimal storage conditions helps in mitigating adverse impacts.
Operational Stress
Excess load and improper usage create undue stress on alloy jaws that can result in premature deterioration.
Overloading the jaws: Exceeding the recommended operational limits compromises structural integrity.
Consequences of improper usage: Incorrect application techniques or rough handling without proper training contributes to unnecessary strain.
Effective Troubleshooting Methods
Troubleshooting alloy jaw issues effectively requires specific techniques and diagnostic tools.
Visual and Manual Inspections
A thorough inspection involves identifying key areas prone to wear and utilizing accurate tools for evaluation.
Key areas to examine: Focus on joints, pivot points, and other regions exposed to repetitive movement.
Tools and techniques for thorough inspection: Use magnifying glasses, calipers, and feeler gauges for detailed assessments.
Diagnostic Tools
Employ advanced diagnostics to ensure comprehensive analysis and avoid missing critical flaws.
Recommended equipment: Portable X-ray units, ultrasonic testing devices, and digital micrometers offer precision insights into hidden defects.
Utilizing technology for better accuracy: Integrate software solutions to log data, predict trends, and automate alerts for scheduled maintenance.
Testing Under Load
Load tests simulate real-world conditions to validate performance post-inspection or repair.
Safe methods to test performance: Gradually increase loads while monitoring stress responses via sensors.
Interpreting test results: Compare metrics against benchmark standards defined by original specifications.
Solutions and Repairs
If issues arise, several remediation strategies can extend usability or restore function.
Re-machining and Resurfacing
Minor wear can sometimes be rectified without full replacement.
When and how to consider re-machining: Opt for re-machining upon noticing small imperfections before they worsen.
Techniques for resurfacing: Employ CNC machinery for consistent accuracy and smooth finishes.
Realignment Procedures
Correcting any deviations ensures optimal operation.
Step-by-step guide: Utilize jigs and fixtures to hold jaws accurately; adjust settings incrementally.
Tools required for realignment: Precision clamps, hydraulic presses, and dial indicators facilitate meticulous adjustments.
Reinforcement and Replacement
At times, replacement becomes inevitable despite best efforts.
Criteria for replacing alloy jaws: Severe cracking, extensive deformation, and irreversible wear demand immediate swap-outs.
Options for reinforcement: Reinforcing with supporting structures or employing higher-grade alloys provides longer-lasting solutions.
Preventive Measures
Proactive steps lessen the risks associated with common problems and enhance reliability.
Regular Maintenance Schedule
An effective schedule balances both routine checks and detailed inspections.
Creating an effective maintenance calendar: Map out tasks bi-weekly, monthly, and yearly depending on usage intensity.
Checklist for routine inspections: Document items like lubrication levels, surface conditions, and any detected anomalies.
Training and Skill Development
Well-trained operators reduce misuse and maintenance mishaps.
Importance of operator training: Educating staff about correct procedures minimizes unnecessary stress on alloy jaws.
Resources for ongoing education: Leverage industry seminars, practical workshops, and certification programs.
Upgrading Equipment
Modern advancements often surpass older models in efficiency and resilience.
Evaluating the need for newer technology: Assess performance gaps where outdated tools cannot fulfill contemporary demands.
Cost-benefit analysis of upgrades: Weigh upfront investment against prolonged service life and enhanced productivity.
Expert Tips and Advice
Sourcing insights from experienced professionals provides insider knowledge that optimizes your maintenance strategy.
Recommendations from Industry Professionals
Insights from seasoned technicians: Practical tips and first-hand accounts reveal what works best in field scenarios.
Common pitfalls to avoid: Forewarning against typical mistakes saves time and resources in troubleshooting processes.
Resources for Further Learning
Expanding knowledge keeps teams abreast of evolving technologies and methodologies.
Books, courses, and online resources: Enroll in specialized courses, read technical literature, and participate in webinars.
Professional organizations and forums: Joining professional bodies like ASME or engaging in community forums builds networks and updates you on latest developments.
Conclusion
Understanding common issues with alloy jaws and implementing effective resolutions require vigilant diagnosis and proactive maintenance. Equipping yourself with the right knowledge and adopting systematic approaches will ensure sustained performance and longevity. Embrace preventive strategies, invest in skill development, and don't shy away from upgrading tools when necessary to minimize downtime and maximize efficiency.
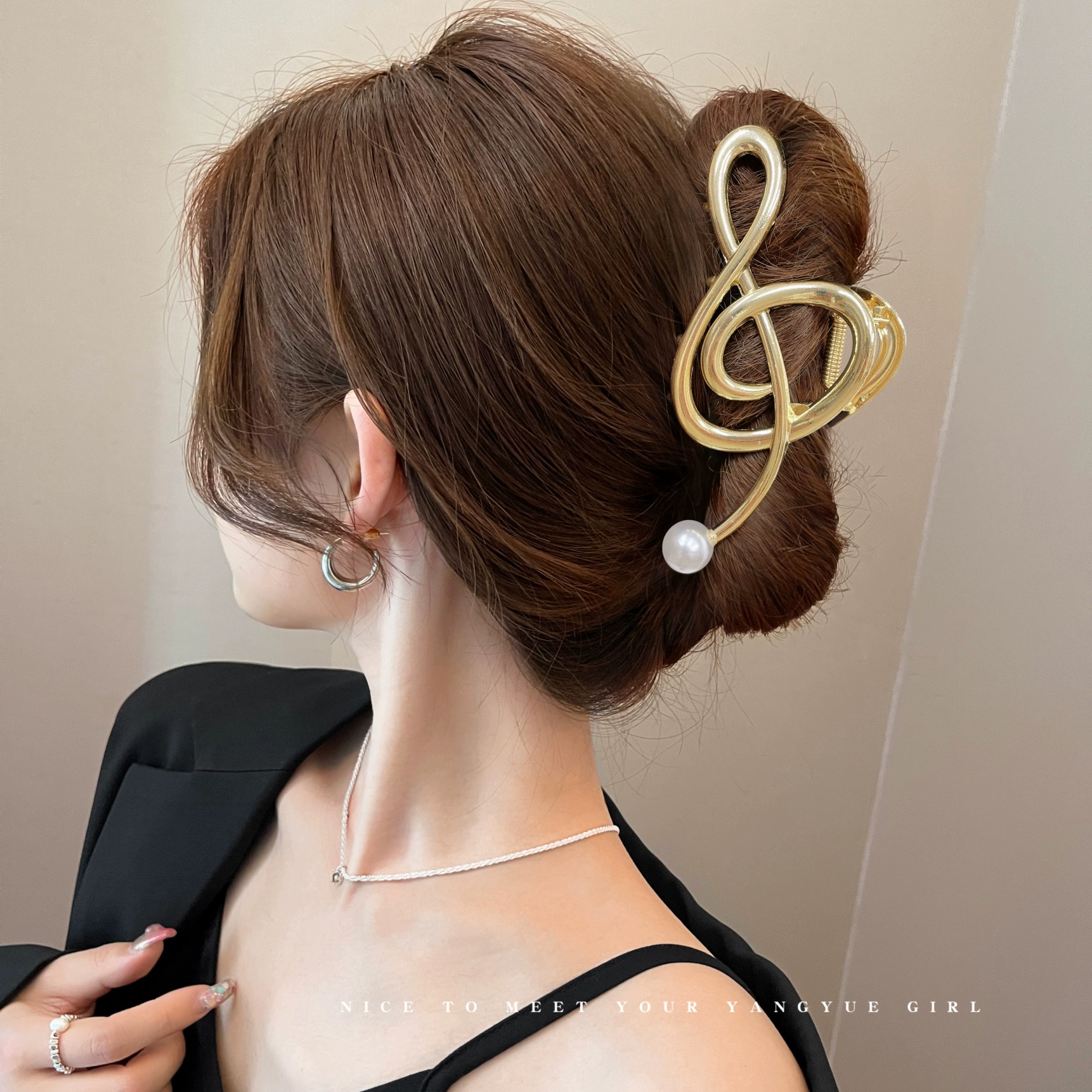