
The automotive industry is continuously evolving, seeking innovations that enhance efficiency and performance while reducing costs and downtime. One such innovation making significant waves is the implementation of alloy jaws. This case study explores a real-world example where alloy jaws have significantly benefited an automotive company.
Background on Alloy Jaws
Alloy jaws are specialized components used extensively across various industries for gripping, holding, or manipulating objects. Typically made from advanced alloys, these jaws offer superior strength, durability, and resistance to wear and tear compared to traditional materials like steel or aluminum. The advantages include enhanced lifespan, better thermal stability, and reduced maintenance needs, which are crucial in high-demand environments such as manufacturing.
Challenges in the Automotive Industry
The automotive industry frequently faces challenges with the durability and performance of traditional jaw materials. Standard materials struggle under continuous stress, leading to frequent replacements, increased downtime, and higher operational costs. Furthermore, the constant need for precision and reliability necessitates components that can withstand extreme conditions without compromising performance. Therefore, there was a pressing need to find solutions that offered enhanced durability and efficiency.
Case Study: Company X
Company X is a prominent player in the automotive industry known for its commitment to quality and innovation. Initially, they faced numerous issues with their traditional jaw materials, including excessive wear, frequent breakdowns, and high maintenance expenses. Realizing the impact on their productivity and costs, Company X decided to explore alternatives. After careful consideration and research, they opted to switch to alloy jaws based on the compelling benefits.
Implementation Process
The transition began with a comprehensive assessment to identify areas where alloy jaws could be integrated effectively. This involved collaboration between Company's internal engineers and external suppliers specializing in alloy technologies. Detailed planning ensured seamless installation into existing systems. Additionally, staff and operators received thorough training to adapt to the new technology, emphasizing safe usage practices and optimal handling techniques.
Performance Metrics and Outcomes
Company X closely monitored several key performance indicators (KPIs) to evaluate the success of alloy jaws. These included production rates, machine downtime, and component longevity. A comparative analysis revealed substantial improvements. For instance, production rates saw a marked increase due to reduced interruptions, while machine downtime decreased notably, contributing to consistent workflow. The longevity of alloy jaws also meant fewer replacements, enhancing overall operational efficiency.
Cost-Benefit Analysis
While the initial investment in alloy jaws was higher than conventional options, the long-term savings proved significant. Reduced maintenance needs lowered ongoing operational costs, and the increased component lifespan translated into fewer purchases over time. Moreover, enhanced production efficiency contributed positively to overall profitability. The cost-benefit analysis highlighted that the benefits far outweighed the initial expenditure.
Employee and Operator Feedback
Feedback from staff and operators at Company X was overwhelmingly positive. Operators noted considerable improvements in daily operations, particularly regarding safety and ease of use. The robust nature of alloy jaws minimized breakage risks, ensuring safer working conditions. Additionally, the reduced need for frequent adjustments or replacements simplified routines, allowing employees to focus more on productive tasks.
Lessons Learned
Several valuable lessons emerged from Company X's successful implementation of alloy jaws. Key takeaways included the importance of meticulous planning and collaboration during the transition phase. Potential pitfalls were avoided through detailed preliminary assessments and close coordination with experts. For companies considering similar upgrades, investing in comprehensive training for personnel and conducting regular performance evaluations are critical recommendations.
Future Prospects
The future of alloy jaws in the automotive industry looks promising, with potential advancements aimed at further improving their properties and applications. Anticipated trends suggest even greater adoption of this technology, driven by continued emphasis on efficiency and sustainability. Early adopters stand to gain significantly, harnessing long-term benefits such as heightened competitive advantage and cutting-edge operational capabilities.
Additional Case Studies
Other notable companies within the automotive sector have also embraced alloy jaws, witnessing similar transformative results. Their experiences reaffirm the advantages observed by Company X, providing additional validation for the widespread integration of alloy jaws. Interested readers can delve deeper into each company's journey through linked detailed reports and articles.
Expert Opinions
Insights from industry experts underscore the growing relevance of alloy jaws. Experts predict broader applications, extending beyond automotive to other sectors requiring high-performance materials. As innovations continue, the role of alloy jaws will likely expand, offering versatile solutions to complex industrial challenges.
Conclusion
In conclusion, Company X's experience exemplifies how the strategic implementation of alloy jaws can lead to remarkable improvements in efficiency, performance, and cost-effectiveness in the automotive industry. Encouraging wider adoption of such advanced materials promises transformative impacts, revolutionizing manufacturing processes and fostering sustainable growth.
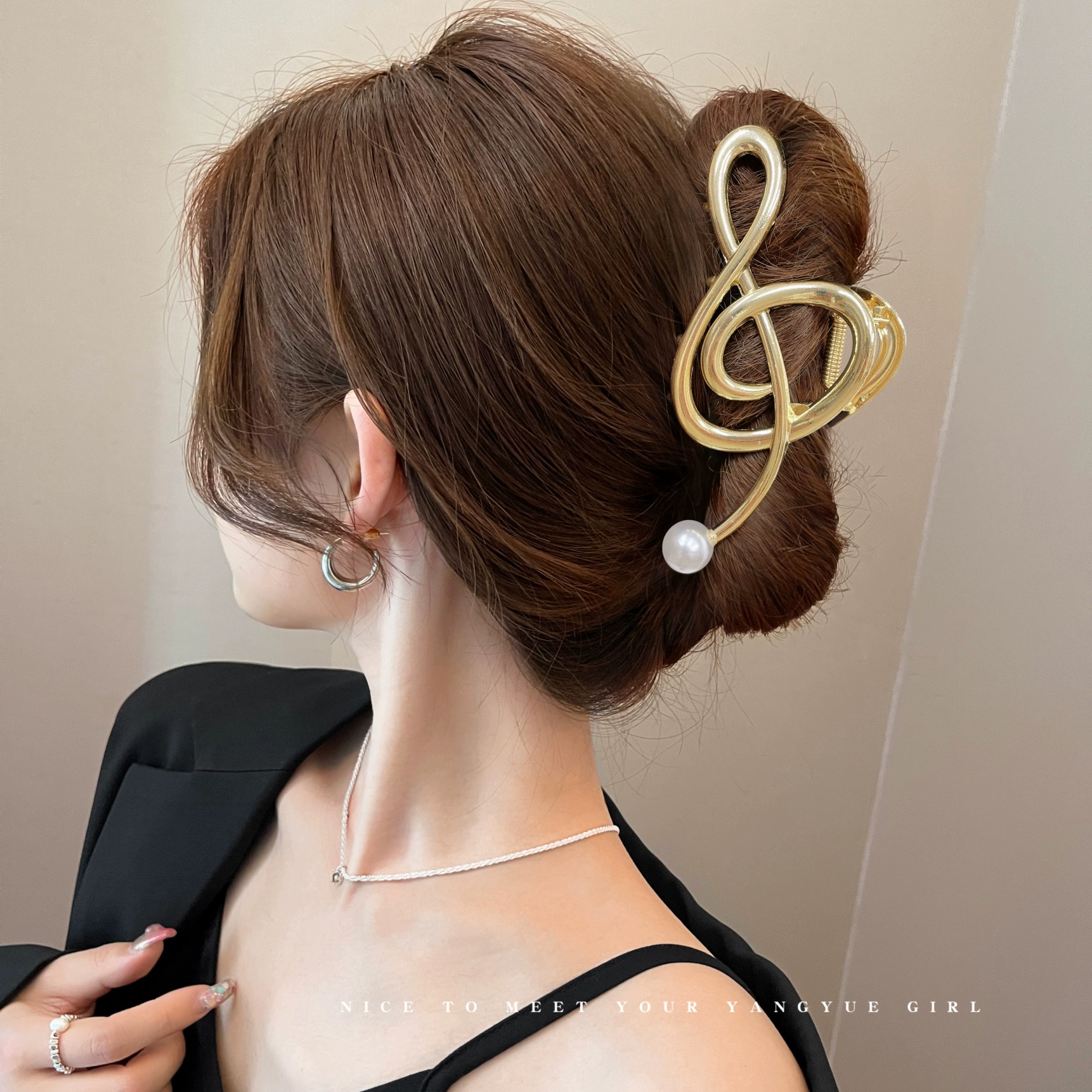