
When it comes to using alloy jaws, even the most experienced professionals can fall prey to common mistakes that compromise the efficiency and safety of their operations. Alloy jaws serve a crucial role in various applications, from machining to manufacturing, by providing reliable clamping force and endurance under extreme conditions. However, overlooking key aspects of their usage can lead to severe consequences. Here are some commonplace errors to avoid when working with alloy jaws.
Choosing the Wrong Alloy Type
Understanding different alloy compositions is pivotal for selecting the correct type for your needs. Each alloy possesses unique properties tailored to specific applications. Mismatching alloy jaws with material specifications not only reduces effectiveness but can also result in equipment damage or failure. Using incompatible alloys may cause detrimental reactions, leading to compromised structural integrity and inefficient operation.
Incorrect Installation Procedures
Proper installation is fundamental for maximizing the performance of alloy jaws. Misalignment during setup can skew productivity and precision. Ensuring proper alignment techniques and secure fastening methods will safeguard against operational discrepancies. It’s vital to adhere to the manufacturer’s guidelines during installation, as overlooking these instructions could void warranties and reduce the lifespan of the jaws.
Overloading the Jaws
A critical aspect often neglected is recognizing load limits. Exceeding the prescribed capacity of alloy jaws results in undue stress that can trigger abrupt failures. The dangers of surpassing load recommendations include distorted materials and potential catastrophic failures. Distributing weight evenly across the jaws helps prevent overburdening any single point, maintaining their functional integrity.
Neglecting Regular Maintenance
Regular maintenance is essential for prolonging the life and utility of alloy jaws. Cleaning and lubrication mitigate wear and tear while ensuring optimal performance. Identifying early signs of deterioration like cracks or corrosion enables timely interventions before major issues arise. Routine inspections help maintain operational reliability and prevent unexpected downtime.
Improper Use of Clamping Force
Calculating the appropriate clamping pressure is another area where users falter. Over-tightening can deform both the jaws and the workpiece, leading to inefficiency and increased operational costs. Varying tasks necessitate adjusting clamping force accordingly to preserve both the machinery and materials being worked upon.
Ignoring Safety Protocols
Safety should always be paramount. Personal protective equipment (PPE) requirements must be adhered to rigorously. Safe operating procedures, such as controlled sequences of operations, minimize risks. Familiarity with emergency stop mechanisms and ongoing training on safety measures protect both human resources and machinery from harm.
Lack of Training and Experience
The importance of specialized training cannot be overstated. Professionals lacking hands-on experience are more prone to committing costly errors. Continuous education and certification programs keep operators updated with best practices and technological advancements in alloy jaw utilization.
Skipping Calibration Checks
Precision in calibration ensures accurate measurements and consistent output quality. Regular calibration checks using appropriate tools and techniques uphold this precision. Skipping these checks leads to deviations in machined parts and reduced product quality.
Using Damaged or Worn-Out Jaws
Inspecting for cracks and defects regularly mitigates the risk of operating with compromised equipment. Continued use of damaged or worn-out jaws can break down unexpectedly, posing threats to both personnel and machinery. Observing replacement guidelines assures compliance with safety standards, enhancing overall efficiency.
Environmental Factors
Temperature and humidity influence the performance and longevity of alloy jaws. Protections against environmental factors such as corrosion through regular upkeep and suitable storage can extend the lifespan of the alloy jaws significantly.
Ignoring Manufacturer’s Recommendations
Manufacturer’s recommendations provide a comprehensive understanding of optimal usage parameters for alloy jaws. Reading and thoroughly digesting user manuals ensures adherence to these guidelines. Sticking to warranty conditions preserves service entitlements. Utilizing available support and resources from manufacturers aids in troubleshooting and enhances operational know-how.
Avoiding these common mistakes fosters safer practices, enhances productivity, and extends the operational lifespan of alloy jaws. By adhering to best practices and remaining vigilant about their application and maintenance, you can optimize the returns on your investment and ensure seamless project execution.
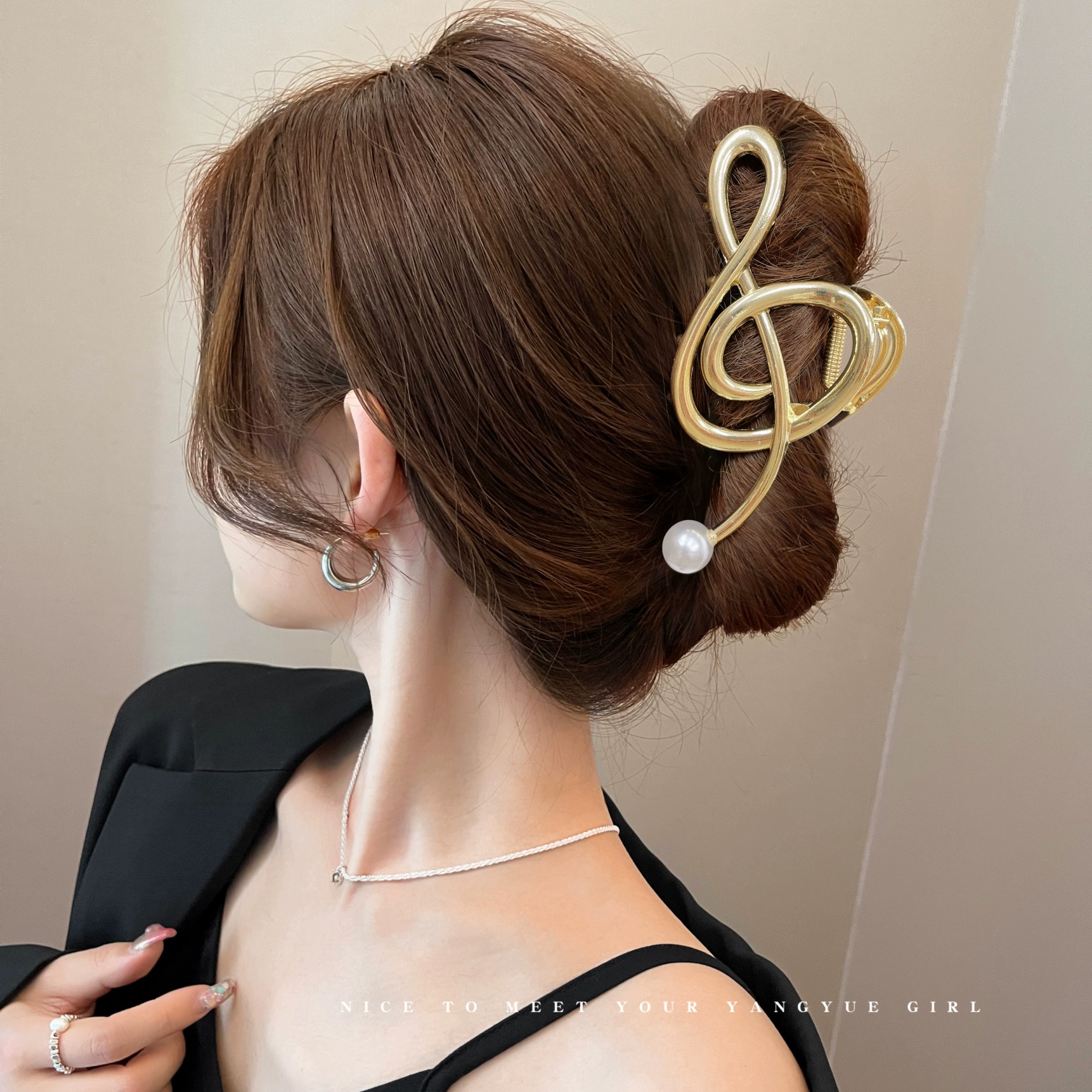